The my23 car was designed with a tripod principle to its powertrain. we planned for a single large motor to power the rear wheels through a sprocket and differential, with two smaller motors mounted directly to the suspension uprights powering each of the front wheels. this would allow for 4 wheel drive while still allowing a functional car in case the software and control electronics to control the front motors was not ready in time for competition. to this end, the front uprights were designed to house planetary gearboxes to increase the motor torque, each with one sun gear and three planetary gears. To ensure the gears did not bind or wear while running, they had to be run-in together before being put into the car.
To achieve this wearing-in, I designed a mount to attach the gearbox to the spindle of our machine shop's Haas CNC mill. we would then run the mill for roughly 250,000 cycles to fully mesh the gears together.
The tool consisted of three parts: a mounting plate, a spindle mount for the sun gear, and a bearing holder to stabilize the spindle.
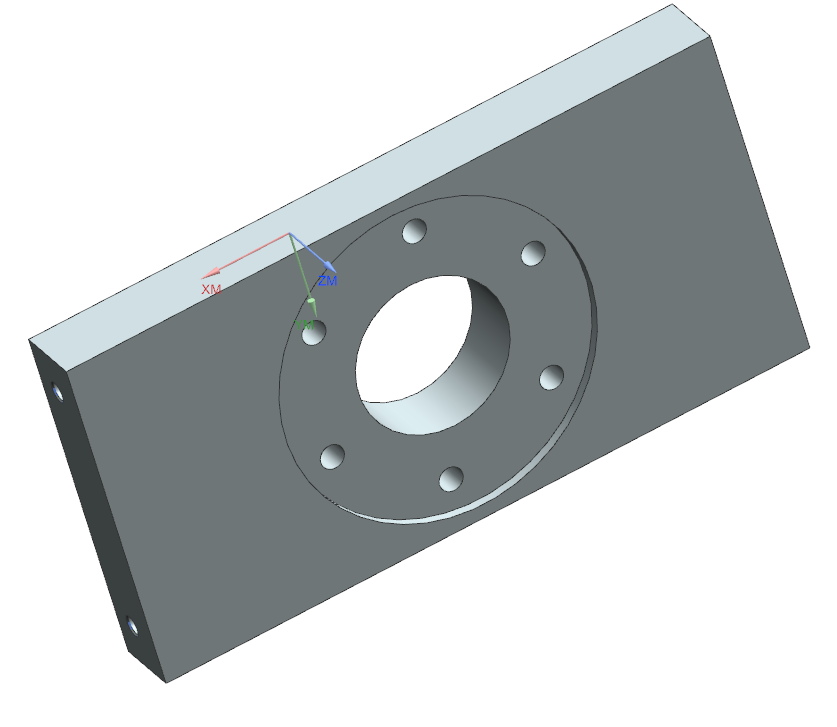
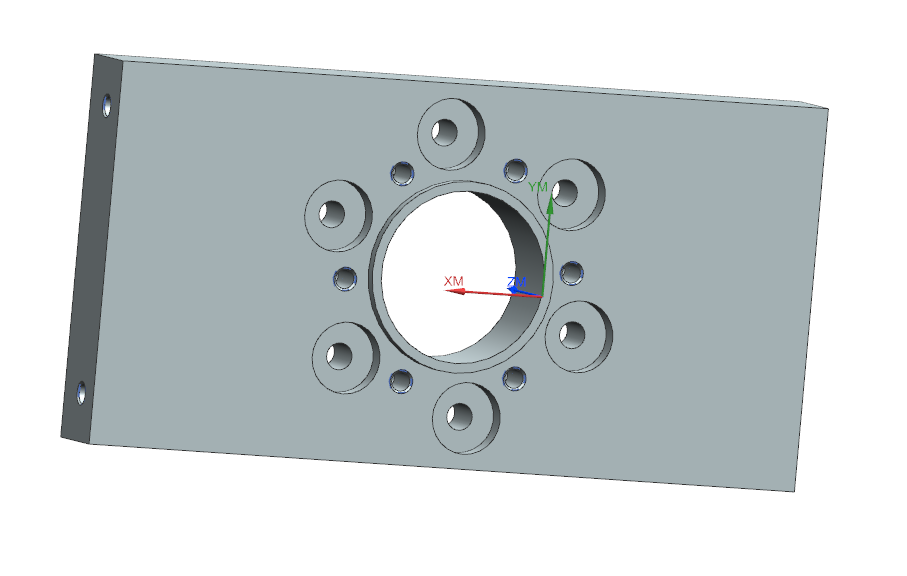
The top of the plate featured a recess to hold the bearing concentric, as well as mounting holes to bolt the holder in. On the sides are holes used to hold the plate in a vice grip inside the CNC mill.
The bottom featured a lip as a locating feature to ensure concentricity with the upright. the recessed mounting holes are clearance holes for 1/4-20 bolts to attach to the bearing holder. the chamfered holes are threaded mounting holes for 1/4-20 bolts to attach through the suspension upright, mounting it to the plate

The bearing holder held the bearing in through a press-fit with 2 thousandths of an inch of interference, as well as positive retention through a lip at the top and the mounting plate at the bottom.
The spindle mount held the sun gear on the end through a slip fit, with a key to constrain the rotation and a snap ring to constrain it vertically. The changing diameters of the shaft allowed it to fit precisely through the bearing and opening in the gearbox while constraining it vertically. It mounted into the CNC spindle via a compliant coupler.
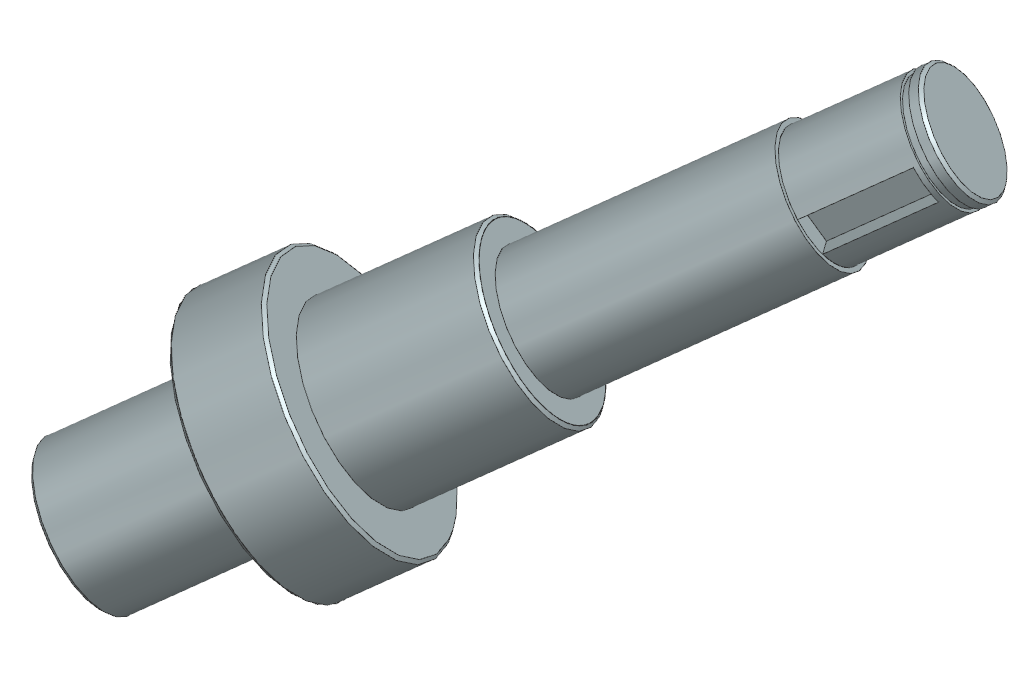
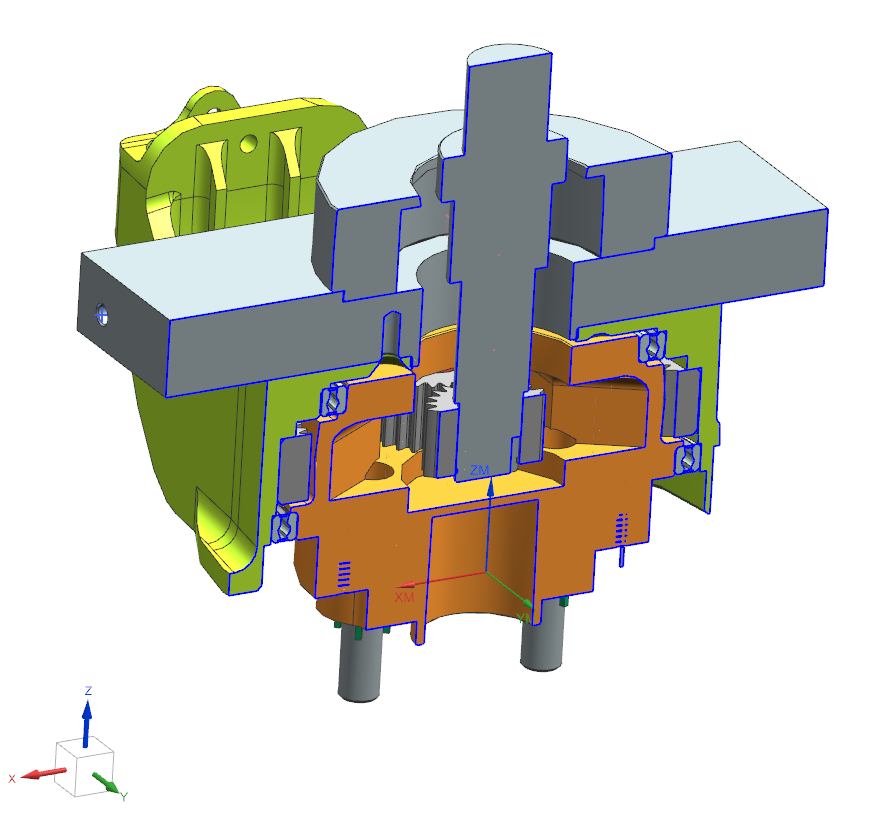
Pictured is the complete assembly, with the suspension upright in green and the gearbox in orange. The spindle shaft fits through the bearing held in the bearing mount, with its sun gear interfacing with the three planetary gears in the gearbox. This whole assembly was held in the CNC with a vice grip and run through a 47-minute spin cycle for 237,000 revolutions, minimizing resistance and binding in the gears.
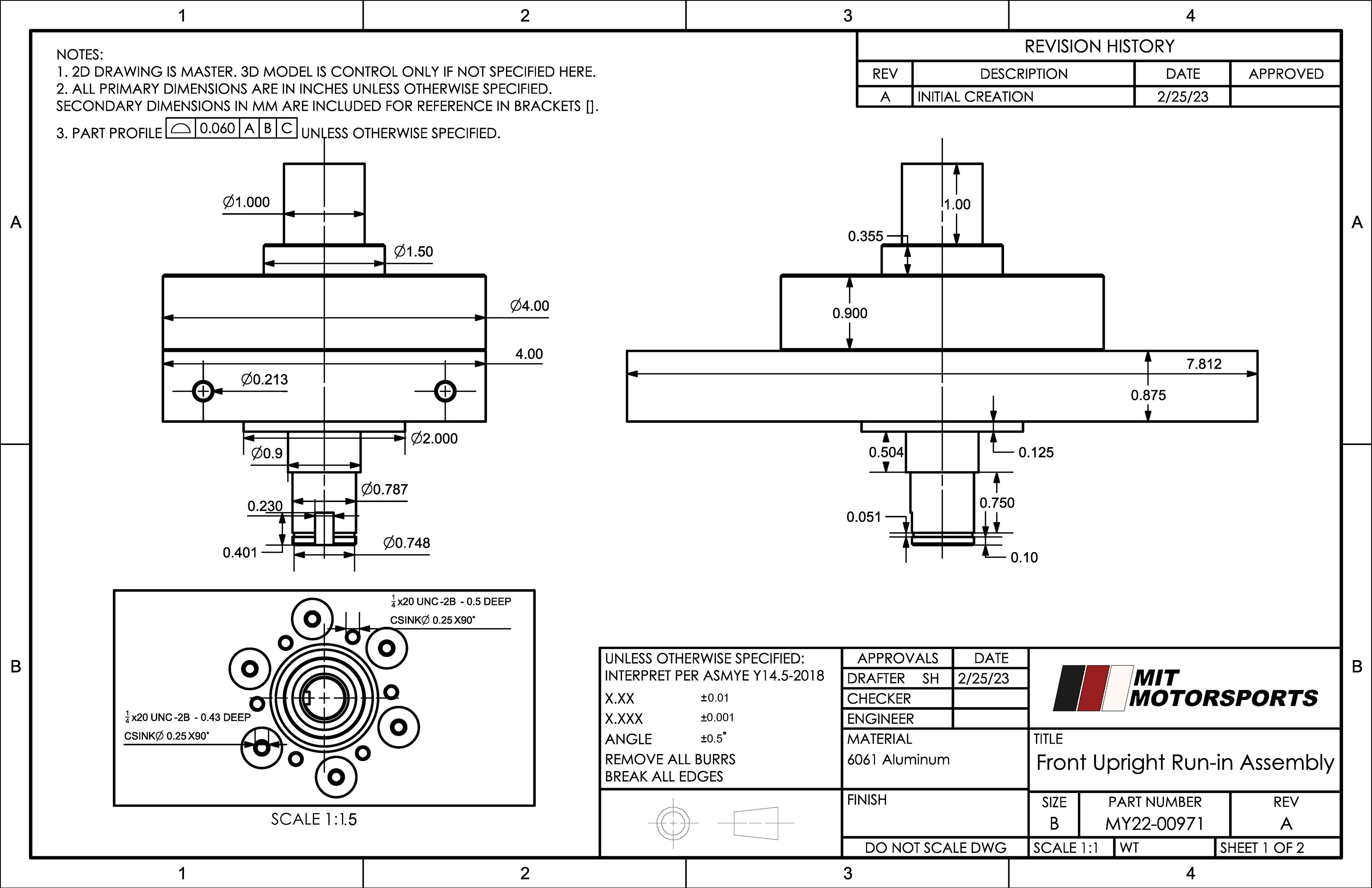
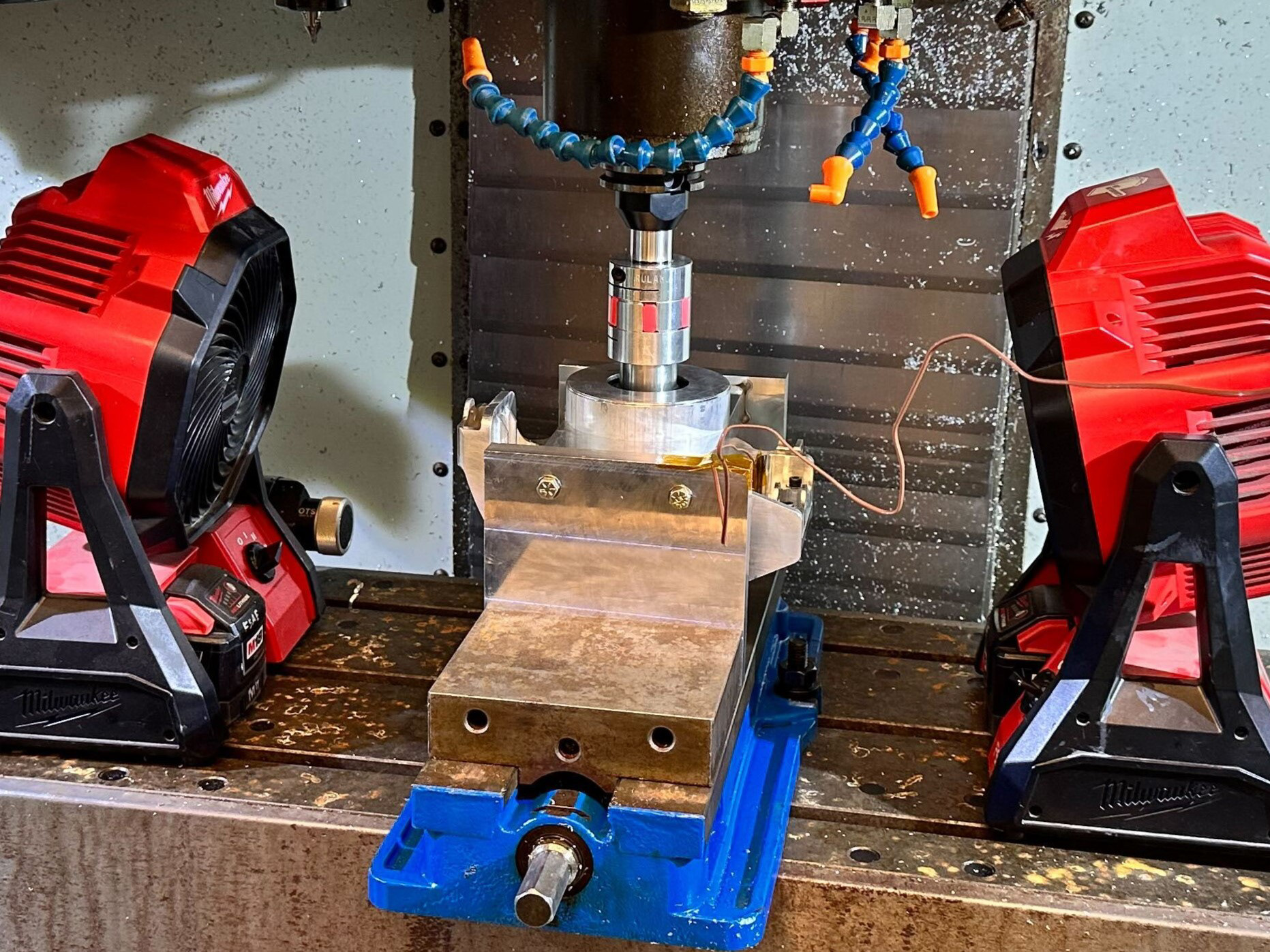
The run-run in setup fixed in our HAAS VF2 CNC machine. Thermocouples are mounted to monitor temperature of the package as the friction of the un-worn-in gears against each other is significant. The fans simulate the forced convection of the airflow over the uprights while driving, as ambient free convection is not sufficient to cool the gearbox package at high speeds for extended periods of time. The setup ran for 125,000 revolutions for this gearbox.